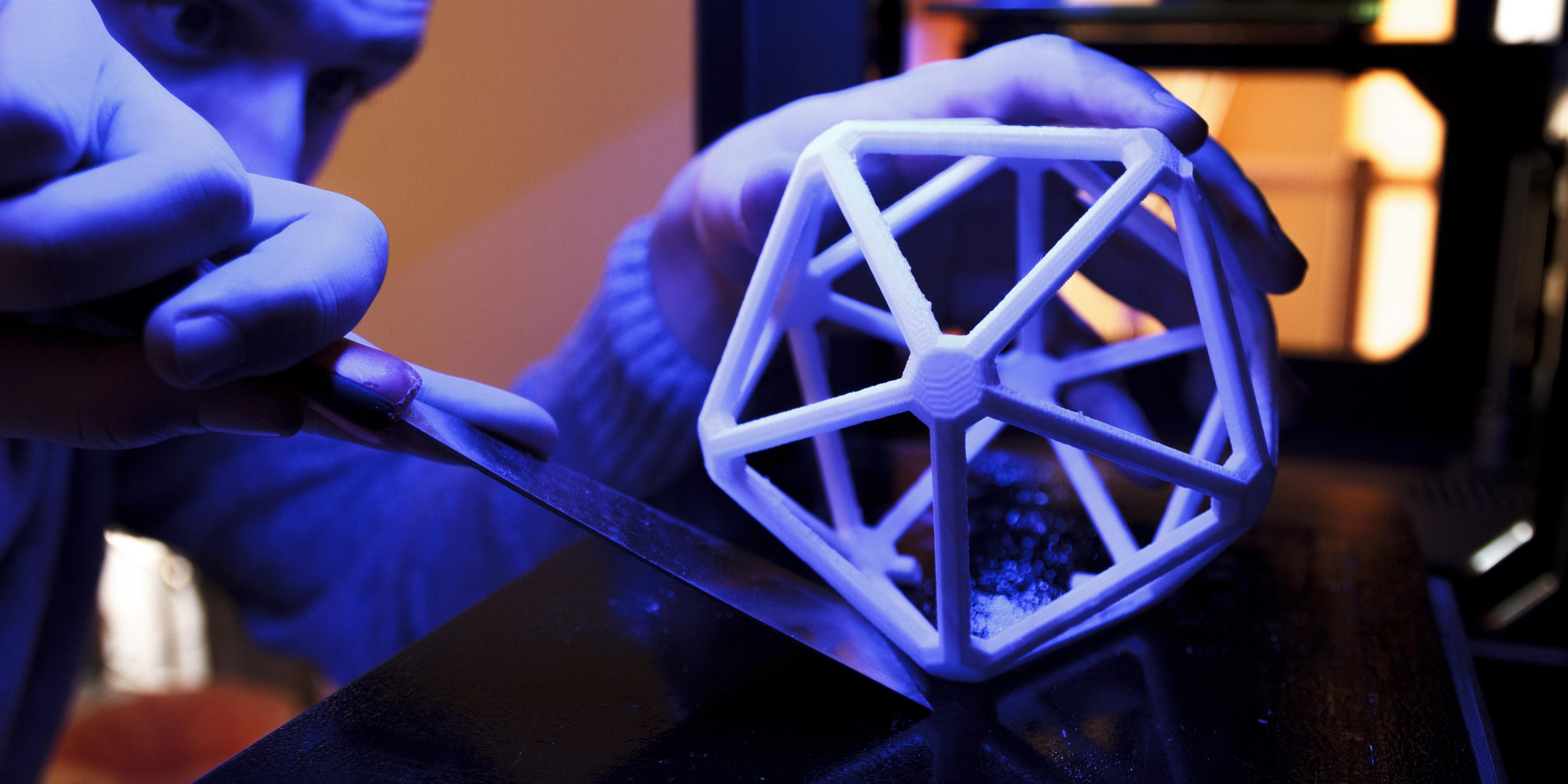
In un mondo pervaso di informazioni sia- mo ormai abituati a farci guidare dai nostri dispositivi digitali nelle scelte quotidiane di acquisto di prodotti e servizi personali. Considerando che in un solo minuto vengono inviati 16 milioni di messaggi WhatsApp e vengono fatte 3,5 milioni di ricerche su Google, si può capire quanto la cosiddetta “digital transformation” sia entrata nella nostra vita di tutti i giorni. Se sul fronte consumer le tecnologie digitali sembrano avere una diffusione più che esponenziale (secondo quanto ipotizzato da Larry Downes e Paul Nunes nel loro libro “Big Bang Disruption”), nel mondo business-to-business (B2B) ci sono ancora grandi spazi di miglioramento. In particolare, nell’ambito manifatturiero la tecnologia digitale non è ancora utilizzata al pieno delle sue possibilità. Pensiamo infatti alla miniera di dati e informazioni, strutturate, semi-strutturate e non che, se correttamente incanalate e analizzate, possono fornire un incredibile supporto alla supply chain e alle operations. Grazie alle tecnologie abilitanti caratterizzanti un’Industria 4.0 molte aziende hanno colto finalmente l’opportunità per confrontarsi con le nuove soluzioni tecnologiche e per digitalizzarsi attraverso l’uso intensivo dell’Internet of Things (IoT), dei Big Data, dei Robot autonomi o collaborativi e della realtà virtuale.Inseguendo i cambiamenti in atto la Liuc Università Cattaneo ha investito nella formazione dei propri ingegneri gestionali, attraverso un piano di studi appositamente studiato per preparare figure professionali che siano confidenti con l’automazione, la robotica, la simulazione e il data analytics.
Ma come è possibile apprendere “in pratica” i nuovi paradigmi del 4.0, sporcandosi le mani con situazioni reali? Per rispondere a questa domanda che in realtà proviene dalle aziende, la Liuc ha sviluppato l’i-FAB, una fabbrica digitale in scala 1:1 che funge da aula didattica innovativa.
Nell’i-FAB studenti universitari in primis, ma anche imprenditori e manager si sfidano nell’assemblare dei calcio balilla, toccando con mano la quarta rivoluzione industriale e i benefici che può portare in abbinamento alla filosofia del lean manufacturing. La linea di assemblaggio è infatti organizzata secondo logiche lean, al fine di dimostrare, da un lato, i vantaggi che le tecnologie digitali possono portare nella gestione delle operations e, dall’altro, di fornire un esempio concreto di fabbrica intelligente.
I nove pilastri del Piano Industria 4.0 vengono raggruppati nel modello didattico della Liuc secondo una logica funzionale: (i) progettazione di stabilimento, (ii) monitoraggio e controllo e (iii) miglioramento continuo.
Nel primo gruppo ricadono:
– Simulazione: rappresentazione digitale della fabbrica fisica grazie alla quale è possibile progettare la linea di produzione e prevederne il comportamento nel futuro così da avere un importante supporto decisionale anche in fase di esercizio.
– Data analytics (prescriptive): modelli di programmazione lineare e di ottimizzazione vincolata per dimensionare le risorse necessarie
– Realtà virtuale: rappresentazione digitale del layout fisico per verificare il dimensionamento degli spazi vuoti, spazi necessari per movimentare componenti, prodotti, attrezzature e operatori.
Nel secondo gruppo rientrano i pilastri di:
– Internet of Things (IoT): l’evoluzione della rete dove le “cose” (oggetti) si rendono riconoscibili e acquisiscono intelligenza. Nell’i-FAB le cassettine contenenti i componenti da assemblare avvisano l’operatore che è necessario rifornirle. I prodotti da assemblare sono dotati di transponder RFID che li rendono riconoscibili e tracciabili. Gli spostamenti degli operatori sono monitorati in modo da ottimizzare il layout di fabbrica, così come sono monitorati i loro parametri vitali al fine di garantire la massima sicurezza anche in ambienti di lavoro in solitudine.
– Data analytics (descriptive & predictive): raccolta dei dati da fonti diverse (es., operatori, transponder RFID posizionati sul prodotto da assemblare, strumenti di lavoro) aggregati in unico grande data-set. Quest’ultimo richiede tecniche non convenzionali per estrapolare, gestire e processare informazioni entro un tempo ragionevole.
– Integrazione: elemento fondamentale per poter comunicare direttamente con le macchine all’interno della fabbrica e poter condividere informazioni con clienti e fornitori.
Nell’ultimo gruppo sono presenti:
– Robot autonomi: robot in grado di rilevare l’ambiente circostante e l’intervento umano. Il robot può svolgere operazioni di assemblaggio e movimentazione prodotti e componenti in totale sicurezza e in collaborazione con l’operatore.
– Additive manufacturing: utilizzo della tecnologia 3D printing per la realizzazione sia di componenti di piccola serie e alta personalizzazione richiesti ad hoc dai clienti, sia di attrezzature per il miglioramento dei processi produttivi che avvengono nell’i-FAB.
Grazie al contributo di numerose aziende partner dell’iniziativa, la fabbrica è attrezzata con alcune tra le più avanzate soluzioni di automazione e con sistemi di raccolta e analisi delle informazioni. L’i-FAB non è solo un’aula, ma è anche un laboratorio esperienziale, dove docenti e ricercatori sviluppano progetti di ricerca applicata e metodologie per progettare e gestire fabbriche sempre più intelligenti.