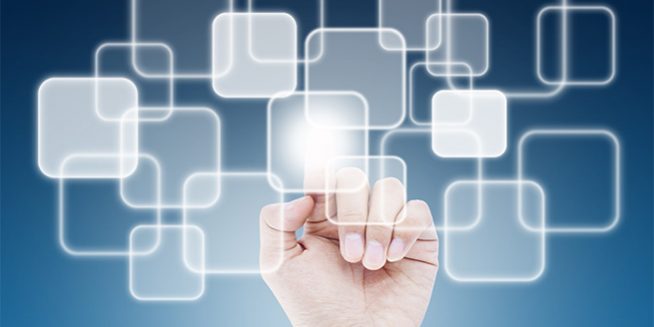
Giuliano Busetto, Presidente Anie Automazione, spiega come le aziende del settore abbiano già abbracciato il cambiamento. Ora la priorità è coinvolgere sempre più le Pmi e dialogare con le facoltà scientifiche affinché i nuovi ingegneri abbiano competenze multidisciplinari e integrate fra loro
Industria 4.0 è il tema del momento. Possiamo veramente parlare di una novità per le imprese di Anie Automazione?
Anie Automazione rappresenta le imprese che forniscono diverse tra le tecnologie abilitanti per la realizzazione dell’Industria 4.0.
Parliamo quindi di componenti hardware, software e di sistemi e soluzioni per l’automazione industriale. È lecito pensare che essendo a monte nella filiera le nostre aziende siano quelle partite prima a ragionare in ottica Industria 4.0. e in effetti molti investimenti sono stati già fatti per arrivare pronti a questo momento, nel quale si sta passando a una fase di effettiva implementazione nel nostro paese. Per noi, quindi, questa trasformazione nel modo di fare manifattura non è una novità e le tecnologie alla base del processo sono pronte per essere utilizzate con efficacia e in completa sicurezza. I nostri clienti, costruttori di macchine e utilizzatori finali, dovranno tener conto di questo passaggio, che richiede veramente un epocale cambio di prospettiva e pertanto questa transizione potrà durare anche alcuni anni; in questo lasso di tempo le tecnologie dovranno continuare nella loro naturale evoluzione alla ricerca di prestazioni sempre migliori e nuovi servizi.
Ci può fare alcuni esempi di come l’innesto delle tecnologie digitali sta cambiando dall’interno le imprese del settore automazione?
In realtà l’Ict è da molti anni entrata in maniera massiva nei processi manifatturieri con risultati notevoli in termini di efficienza e sicurezza. Si pensi alla straordinaria importanza che ricopre il software oggi rispetto a pochi anni fa.
Non più solo programmi gestionali per le attività amministrative, logistiche e per la rete di fornitura e di vendita, ma integrazione tra questi livelli e le attività di progettazione, ingegnerizzazione e produzione, oltre a tutti i progressi fatti nel campo della manutenzione.
Chiaramente l’Industria 4.0 vedrà ancora una maggiore integrazione sia a livello di processo produttivo, sia a livello di catena del valore, con un ricorso sempre più importante al cloud e una disponibilità sempre maggiore di informazioni utili a migliorare ancora di più il “time to market” e la flessibilità produttiva.
Questa seconda parte del percorso è, però, appena iniziata e per ora solo alcuni importanti gruppi industriali manifatturieri in Italia possono dire di avere effettivamente già operative delle esperienze Industria 4.0.
Aggiungerei che è anche molto importante in questa fase l’attività di comunicazione e formazione dei manager e degli imprenditori per spiegare i nuovi concetti della fabbrica digitale e per permettere anche nelle imprese più piccole, che costituiscono gran parte del tessuto industriale nostrano, il passaggio alla nuova manifattura.
Quali benefici evidenziano – in termini ad esempio di tempo, precisione, affidabilità – gli imprenditori che applicano le tecnologie digitali?
I tre pilastri della smart factory sono la riduzione del “time to market”, l’aumento della flessibilità nella produzione e l’efficienza, non solo energetica ma in generale dei processi. È chiaro che il semplice utilizzo di un software o di uno strumento basato sul cloud non è sufficiente a garantire tutti questi benefici, ma il modello di Industria 4.0 – se correttamente implementato – può assicurare a imprenditori e manager risultati importanti per il miglioramento della loro competitività.
Ascoltando le imprese di alcuni territori particolarmente industrializzati, nel nostro paese emerge chiaramente una doppia velocità tra le esigenze degli imprenditori che sono perfettamente in linea col modello Industria 4.0 e la comprensione delle più moderne tecnologie per la digitalizzazione, che spesso sono ancora oggi completamente ignorate o comunque poco conosciute.
Anche termini che per la nostra associazione sono ormai quasi scontati, come Internet of things, Additive manufacturing, Big data, Analytics, risultano spesso quasi sconosciuti quando si scende a livello più operativo e si entra nelle aziende medio piccole, che poi compongono la maggior parte del tessuto produttivo italiano.
Quali input darebbe alle facoltà scientifiche per migliorare la formazione del capitale umano?
Come associazione abbiamo da tempo avviato una importante collaborazione con diversi atenei, specialmente le facoltà di ingegneria, perché il settore dell’automazione manifesta da sempre l’esigenza di risorse qualificate e l’università negli ultimi anni ha prodotto meno laureati del necessario. Abbiamo, per esempio, realizzato un format itinerante per spiegare la progettazione meccatronica, ovvero la convergenza tra meccanica, elettronica e informatica e organizzato eventi di tipo motivazionale per spiegare agli studenti cosa significhi lavorare nel mondo dell’automazione.
Fermo restando la competenza verticale, chiediamo ai Politecnici di considerare anche insegnamenti orizzontali, cioè multidisciplinari, formando sempre più ingegneri con competenze di meccanica, automazione, elettronica e Ict integrate. Oltre agli input tecnici relativi ai programmi di studio, mi sento di dire che una maggiore collaborazione tra industria e università con programmi scuola-lavoro più evoluti potrebbe portare a un rapido incremento della qualità e quantità delle risorse formate dall’università e andare incontro a quelle che saranno le esigenze dell’industria manifatturiera a fronte della trasformazione 4.0.
È indubbio che ci sarà una forte esigenza di formare nuove competenze che dovranno essere in grado di gestire i nuovi paradigmi applicati nell’industria a livello mondiale. La fabbrica 4.0 non sarà fonte di perdite occupazionali, ma creerà nuove figure professionali e l’università dovrà adeguarsi rapidamente al cambiamento.