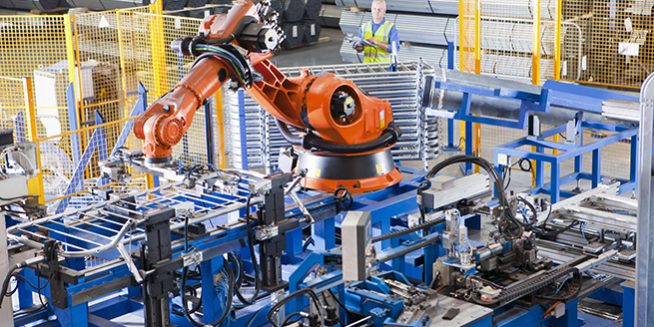
L’approccio più corretto A industria 4.0 è quello di agire in modo mirato e graduale, consentendo l’evoluzione tecnologica dei macchinari.
Industria 4.0 è il tema di più stretta attualità. In quali delle 11 tecnologie ricordate da Federmeccanica nella sua recente indagine, le imprese metalmeccaniche si presentano già strutturate?
Innanzitutto ben due terzi delle imprese campione oggetto dell’indagine dichiarano di aver adottato almeno una delle 11 tecnologie. Al primo posto per conoscenza e applicazione c’è la cybersecurity – nelle sue diverse forme e modalità – seguita dalla robotica e dalla meccatronica. La conoscenza delle altre è minore, ma uno degli scopi dell’indagine è stato proprio quello di “misurare” il grado di applicazione delle tecnologie emergenti al fine di poter intervenire sugli eventuali gap.
Perché un imprenditore del settore metalmeccanico non può permettersi di ignorare l’innesto delle tecnologie digitali nei processi produttivi?
Un dato dell’indagine lo evidenzia chiaramente: le imprese che adottano le tecnologie del digitale hanno performance migliori. Ad esempio, esportano una quota superiore del loro fatturato, investono maggiormente nel capitale umano, nella formazione, nella collaborazione con le università e i centri di ricerca. E lo fanno perché sono consapevoli che questi sono i fattori decisivi per competere sui mercati globali.
La grande trasformazione che molti definiscono “la quarta rivoluzione industriale” è ben rappresentata da alcuni macro trend: 20 anni fa meno dell’1% della popolazione mondiale era connesso in rete, dieci anni fa era il 15% e oggi siamo al 75%.
Le persone connesse sono dentro un mondo sempre più digitale, al punto che nel 2025 si stima che vi saranno più di 50 miliardi di dispositivi collegati alla rete. È un gigantesco cambiamento che interessa tutte le dimensioni dell’agire umano: dal modo di apprendere al modo di lavorare, fino al modo di avere cura di sé. In questo quadro le aziende del settore metalmeccanico possono ottenere enormi risultati dall’applicazione di queste tecnologie in tutto il processo industriale.
Ci può fare alcuni esempi concreti di come questi ultimi stanno cambiando?
Ci sono ormai diversi esempi anche nel nostro paese di come l’applicazione delle tecnologie oggetto dell’indagine stia modificando il modo di lavorare delle nostre imprese. Ad esempio, il crescente utilizzo di dati forniti dalle stesse macchine utilizzate all’interno del processo produttivo per gestire in modo più efficiente l’attività di manutenzione anche predittiva delle stesse o il miglioramento delle loro perfomance. O, ancora, l’applicazione dei principi della cybersecurity all’insieme dei processi aziendali a maggior criticità. O l’uso crescente della robotica collaborativa anche in ambiti più ampi di quelli strettamente industriali.
Siamo comunque di fronte a una “trasformazione” che non comporta la necessità di “cambiare tutto buttando via tutto”, eliminando ciò che si è creato in anni e anni di sacrifici e investimenti. Anzi, vi sono molte testimonianze virtuose di come si possa operare in maniera graduale, adoperando macchinari e impianti già esistenti, andando ad agire con interventi mirati che, a costi sostenibili, ne permettano un’evoluzione digitale. Tutto ciò è fondamentale per garantire sostenibilità e concreta attuazione a tale processo.
La quarta rivoluzione industriale promette di valorizzare ancora di più le persone. Come gli imprenditori del vostro settore stanno sensibilizzando i collaboratori rispetto al tema?
Il fattore umano è decisivo per il successo di questa “grande trasformazione”.
Le risorse umane saranno sempre più qualificate e affiancate da lavoro a basso valore aggiunto o ripetitivo, svolto invece sempre più da macchine. E la persona con la “P maiuscola” sarà ancora una volta beneficiaria e al centro di questa nuova epoca. Ecco perché serve investire sulle competenze – vecchie e nuove – ma serve soprattutto sviluppare le cosiddette “soft skill”, le quali consentono ai nostri collaboratori di adattarsi a scenari complessi e mutevoli allo stesso tempo.
È necessaria anche una grande azione per lo sviluppo delle competenze tecniche associate al digitale in tutti i gradi dell’istruzione, servono nuove professionalità e managerialità. Basti pensare ai “data analyst”, che dovranno aiutare le imprese nel “governare” i miliardi di dati prodotti dalle nuove filiere produttive o ai servizi di “pre e post-sale” in nuove forme di relazione con i clienti e i consumatori finali.
Siamo chiamati a diffondere una nuova cultura. Dobbiamo fare sì che coloro che non hanno ancora adottato tecnologie o che guardano con diffidenza e preoccupazione a questi cambiamenti ne possano comprendere i benefici per la loro azienda. Per questo stiamo lanciando un grande programma di iniziative volte a sensibilizzare tutte le nostre imprese, dalla più grande alla più piccola, sulle opportunità della nuova “Fabbrica intelligente”. Pensiamo che questa “rivoluzione” industriale possa essere in realtà una “evoluzione” verso una nuova dimensione di fabbrica, se saremo in grado di comprenderla fino in fondo e di accompagnare questo fondamentale percorso di cambiamento cogliendo le opportunità nell’interesse delle imprese, delle persone e del paese.