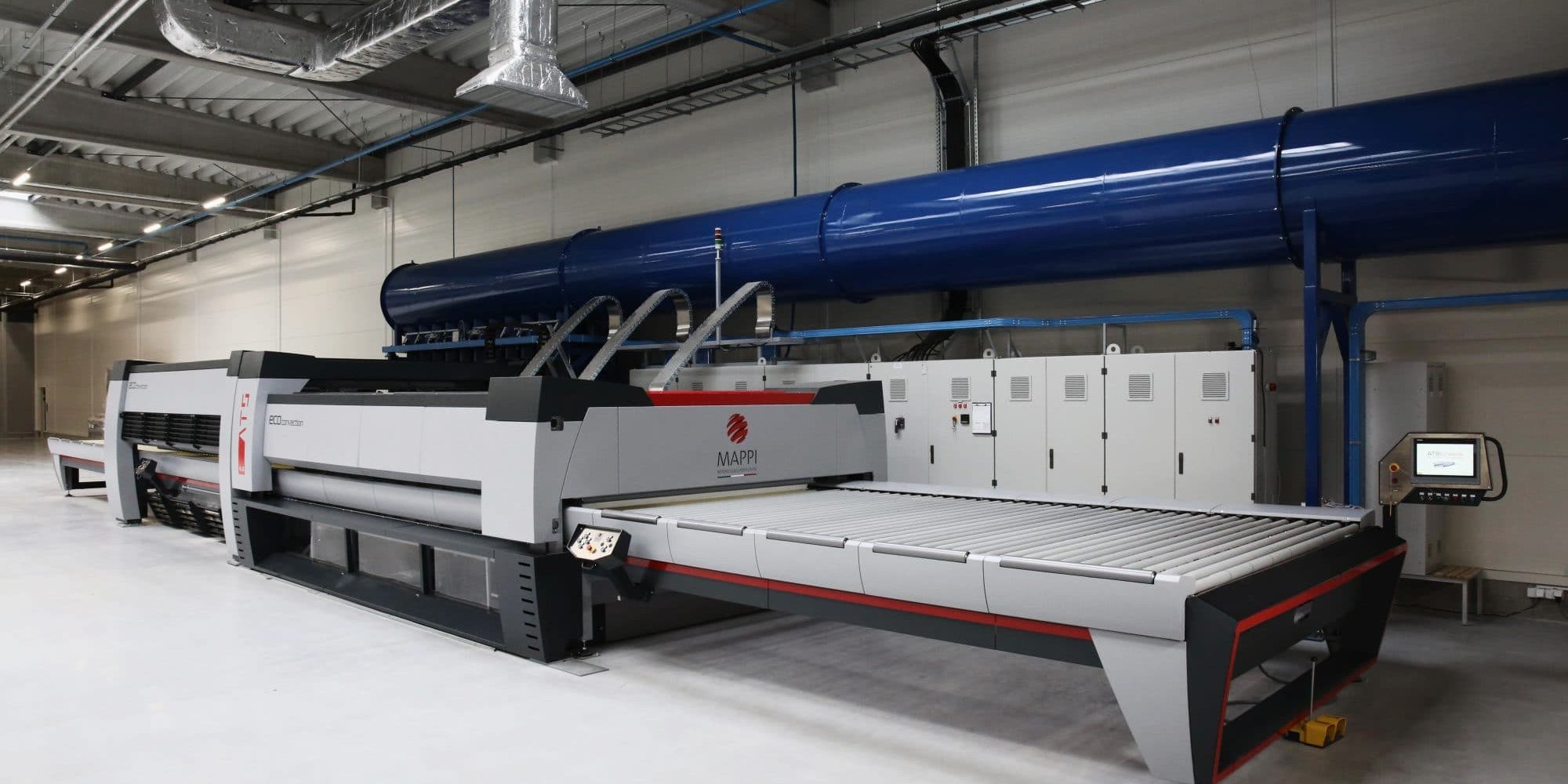
Il procedimento tecnologico che, a partire dal 1993, ha consentito alla Mappi International – 8,5 milioni di euro di fatturato nel 2020 e 58 dipendenti – di diventare leader nel campo della produzione di forni per la tempra del vetro piano non è certo banale. Per ottenere dall’uso dei macchinari dell’azienda di Cisterna di Latina (Lt) una qualità superiore alla media bisogna infatti riuscire a portare le lastre a 700 gradi, ma, soprattutto, a raffreddarle poi di colpo senza che queste si rompano o presentino imperfezioni.
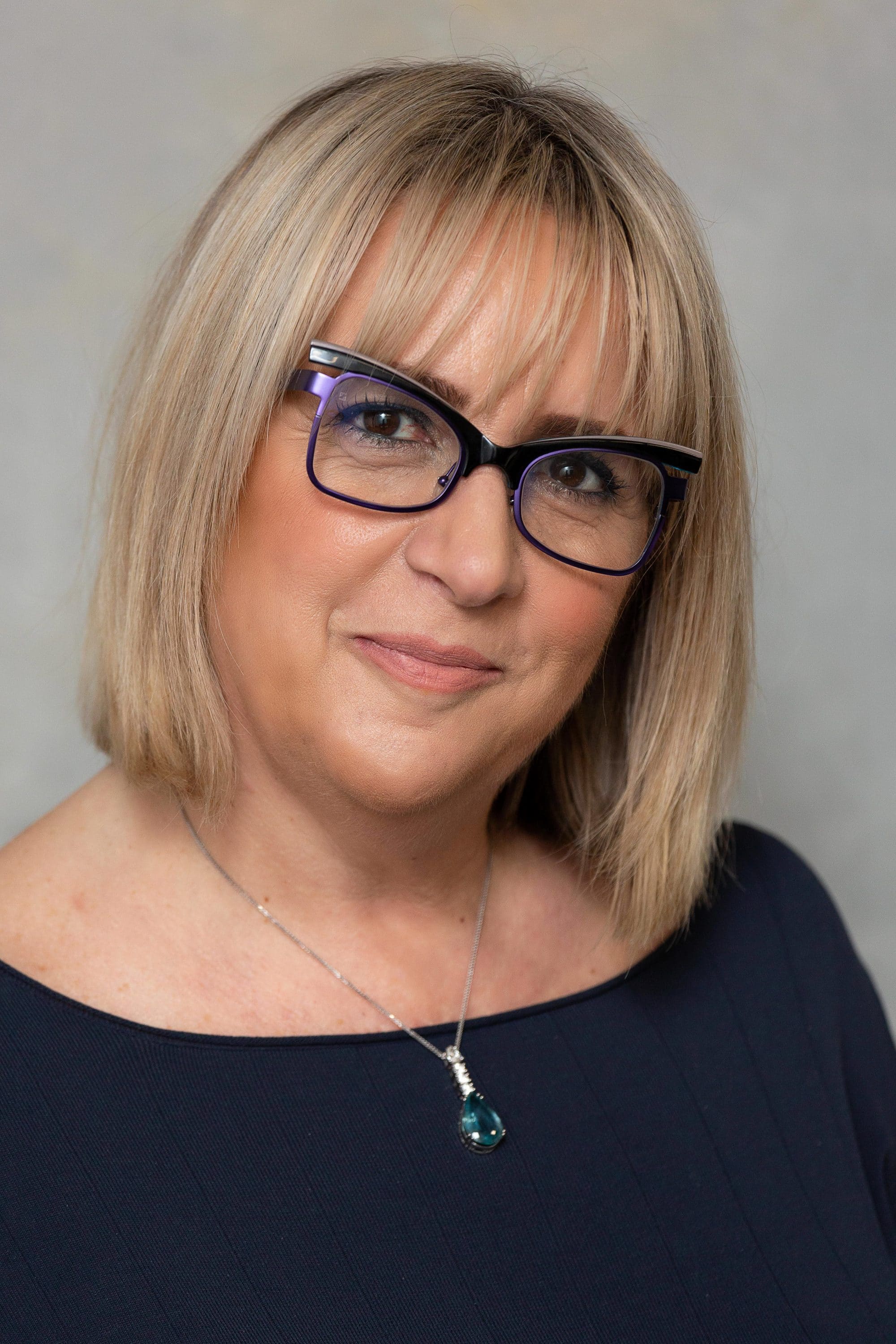
NANCY MAMMARO
“Al termine di questo tipo di lavorazione il vetro temperato diventa sei, sette volte più duro di uno normale e quando si rompe, magari un parabrezza di un’auto, lo fa in tanti piccoli pezzettini senza ferire chi è dentro l’abitacolo”, spiega Nancy Mammaro, socio unico e amministratore della Mappi International.
La mission di Mappi è quella di dare sicurezza assoluta ai clienti, di garantire loro affidabilità e precisione quando acquistano un macchinario che può produrre vetro anche 24 ore su 24, potendo inoltre mettere sul piatto commerciale un ottimo risparmio energetico. “Come molte Pmi italiane siamo concentrati su un mercato di nicchia, ma questo impegno ci sta ripagando, perché, per esempio, non è inusuale che ci sia chi ci contatta anche per telefono per comprare un prodotto da oltre 500mila euro. Si fidano di Mappi, insomma, e questa è una soddisfazione veramente grande considerato che in passato abbiamo, tra l’altro, rifiutato per due volte le avances di aziende straniere pronte a rilevare la proprietà”.
Sfida che giornalmente si ripresenta all’interno dello stabilimento di Cisterna, quartier generale di un’azienda in grado di essere protagonista in varie zone del mondo, oltre che in Italia. “In Sicilia praticamente tutti i forni per la tempra presenti sul territorio sono prodotti da noi, mentre siamo molto attivi anche in Centro e Nord America. In particolare, in Canada, Messico e Stati Uniti, dove abbiamo scelto di stabilire la nostra seconda casa. È a Naples, in Florida e ci consente di occuparci più capillarmente di un mercato che conosco bene, essendo nata negli Usa dove vive tutt’ora una parte della mia famiglia”.
Questo aspetto ha sicuramente aiutato la crescita esponenziale di Mappi oltreoceano. “Solo tra costa Est ed Ovest si contano non meno di un centinaio di macchinari prodotti da noi. Più di vent’anni fa abbiamo provato ad inserirci nel mercato americano e fortunatamente da questa sfida siamo usciti vincitori”, commenta l’amministratore delegato della Pmi laziale.
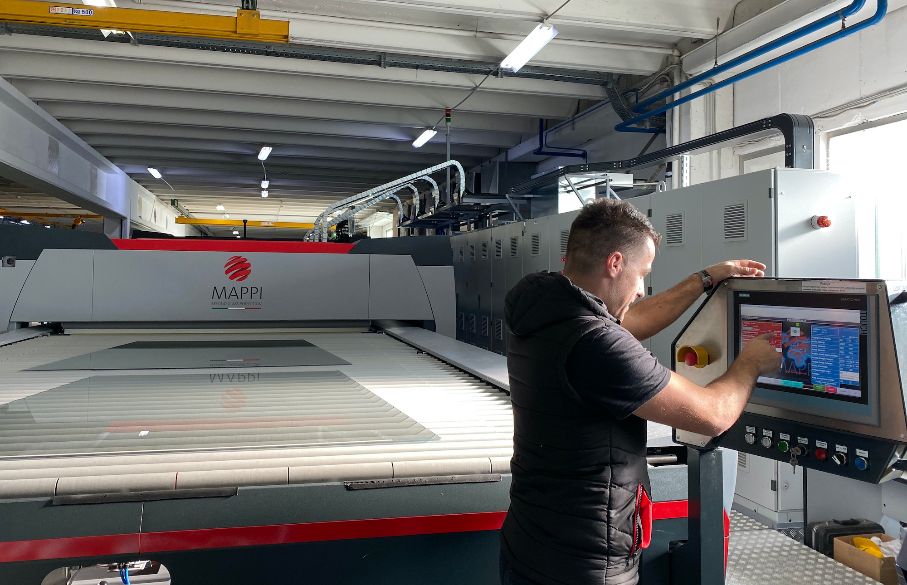
UNA FASE DELLA LAVORAZIONE
Forni tecnologicamente avanzati, sempre al passo con i tempi, ma che la Mappi cerca di rendere fruibili a tutti. Innovazioni, come sottolinea Nancy Mammaro, che si presentano sufficientemente semplici agli occhi della clientela. “In giro per il pianeta ci sono 400 macchine della Mappi e per metterle in opera non ci vogliono conoscenze tecniche eccessive – chiarisce Mammaro –. Inoltre, consumano il 50% di elettricità in meno rispetto agli altri anche per merito di un software dedicato, avendo un prezzo d’acquisto leggermente superiore alla concorrenza. Ma per costruire questo tipo di macchine servono almeno 3mila ore di lavoro e perciò il costo maggiore ha motivazioni ben precise”.
Successo che la clientela riconosce all’azienda pontina, orgogliosa di poter mettere in campo un brand con un’idea precisa all’origine. “I materiali che servono per produrre i nostri forni li acquistiamo non oltre i confini europei e il resto lo facciamo tutto in casa, anche perché possiamo contare sui migliori tecnici al mondo. Che vengono in gran parte dal settore della lavorazione del marmo, dove siamo da sempre un’eccellenza”.
E mentre continua a girare l’Italia e il mondo per proporre i suoi forni e mantenere i contatti con chi ne ha già uno, Nancy Mammaro è già con la mente sul nuovo progetto aziendale. Quel vetro Super Temper, prodotto altamente innovativo, in grado di assicurare prestazioni elevate sempre nel solco dei dettami dell’industria 4.0. “È un qualcosa di particolarmente evoluto, ma comunque user friendly, che si colloca nel segmento dei vetri tagliafuoco – conferma Mammaro –. Il mercato ce lo chiedeva da tempo: permette di produrre il vetro in maniera più veloce, economica ed efficiente”.