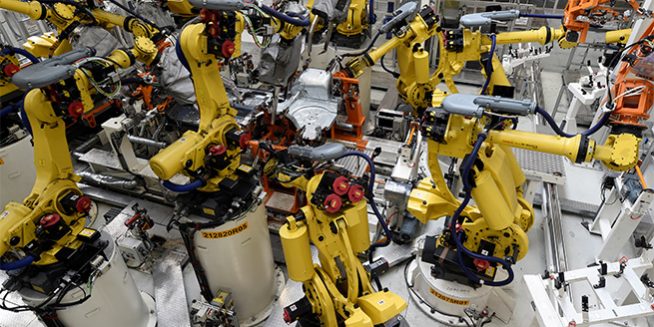
Come noto l’Industry 4.0 è un paradigma industriale nato all’interno delle aziende automobilistiche tedesche e da queste diffusosi agli altri settori industriali con lo scopo di trasformare radicalmente la produzione, passando da sistemi produttivi interconnessi localmente a flussi produttivi integrati, automatizzati e globalmente ottimizzati.
Tale paradigma è giustamente considerato la quarta rivoluzione industriale: dopo l’introduzione nei processi di produzione della forza vapore, di quella elettrica e, infine, dell’automazione, siamo all’alba di un complesso cambiamento all’interno delle fabbriche. Questo, infatti, non è basato come i precedenti su una specifica tecnologia, bensì sulla combinazione di alcuni elementi tecnologici, che hanno l’ambizione di rendere le fabbriche “intelligenti” e in grado di funzionare in modo cooperativo con l’uomo.
Molti dei concetti connessi all’Industry 4.0 o alla “fabbrica digitale” in realtà erano presenti già da qualche anno, ma ciò che mancava era un termine che li comprendesse tutti insieme. Altri, invece, come i self-driving vehicle o i robot collaborativi rappresentano un’evoluzione di tecnologie consolidate cui si è aggiunta la possibilità di immagazzinare, scambiare e condividere i dati di funzionamento grazie all’incredibile evoluzione dei sistemi di riconoscimento, conservazione e scambio delle informazioni.
Quando si dice che il paradigma Industry 4.0 è nato all’interno delle aziende automobilistiche tedesche ci si dimentica che tali aziende, come tutte quelle del settore automotive, operano seguendo principi del lean manufacturing derivati dal Toyota Production System.
Processi produttivi e logistici snelli sono un prerequisito fondamentale per l’implementazione della “fabbrica intelligente”. Automatizzare o governare processi complessi sfruttando le tecnologie digitali, oltre a essere estremamente difficile e oneroso, rende il sistema logistico-produttivo rigido e, al contempo, poco robusto.
Se si pensa alla logistica per una fabbrica 4.0 viene spontaneo associarla ad un’automazione spinta, all’assenza di personale e alla forte ripetitività delle operazioni svolte. Tuttavia i paradigmi produttivi lean vedono la drammatica riduzione dei lotti e la necessità di una grande reattività e capacità di adattamento ai cambiamenti.
Ecco che allora diventa fondamentale avere un’automazione snella. Questo perché con la crescita del mass-customization, occorre pensare a fabbriche in grado di gestire singoli ordini con produzioni quasi unitarie, il cui lotto minimo non è più calcolato per saturare gli impianti, ma è derivato dalla necessità di soddisfare in poco tempo le esigenze del singolo cliente.
Nella fabbrica del futuro anche i processi logistici di magazzino saranno facilitati dall’introduzione di sistemi automatici di movimentazione e stoccaggio, in grado di parlare tra di loro. Fortunatamente le soluzioni migliorative oggi non mancano e la tecnologia sta diventando sempre più pervasiva anche nei magazzini, grazie agli stimoli del Governo in tema di automazione (come il “superammortamento”). Dai veicoli a guida autonoma in grado di autoregolarsi in funzione delle dinamiche del magazzino, ai sistemi di materials handling automatici o semi-automatici per le attività di movimentazione, stoccaggio, picking e imballaggio.
Oggi i progettisti, formati nelle scuole di ingegneria industriale (la versione hard dell’ingegneria gestionale), possono offrire soluzioni su misura in grado di integrare interconnessioni di sistemi diversi, di controllare flussi in entrata e uscita ed evadere richieste in tempo reale, ricavando da ogni passaggio informazioni utili a guidare i processi.
Grazie alla smart automation, la logistica di stabilimento faticosa e monotona si trasforma in una elegante danza di “macchine” che si scambiano segnali e comunicano tra loro. Ma le informazioni che guidano l’ottimizzazione dei processi non sono solamente quelle che si trovano all’interno della fabbrica. La logistica, infatti, è storicamente legata al mondo della distribuzione e dello stoccaggio delle merci.
In un mondo sommerso da un oceano di Big Data c’è chi elabora delle previsioni di vendita e pianifica i rifornimenti dei magazzini in anticipo a partire dalle impronte digitali che lasciamo sul web. In realtà non si tratta di prevedere i comportamenti del singolo utente, bensì di stimare con quale probabilità un certo articolo verrà richiesto nel prossimo weekend in una certa area di mercato che è rifornita a partire da un determinato magazzino. Se l’articolo in questione supera una soglia di click da parte dei clienti che vivono nella medesima area, il modello di “logistica predittiva” prevede che un certo numero di pezzi di quell’articolo vengano trasferiti dallo stock centrale all’hub periferico, prima che venga emesso un eventuale ordine da parte dei clienti.
Questa è una delle tante idee messe a punto da Amazon, la più grande e innovativa azienda di logistica del pianeta. Visitando all’interno uno dei magazzini del colosso dell’e-commerce si ritrovano numerose affinità con le fabbriche automobilistiche giapponesi. In un magazzino che deve poter evadere in meno di 24 ore un regalo di compleanno (neanche fosse un farmaco salvavita), nulla può essere lasciato al caso.
Ecco allora che per facilitare la riconoscibilità di oggetti, spazi, attrezzature e persone si usano soluzioni “poka yoke”: segnando a terra i percorsi con strisce colorate, impiegando cassette di sei diversi colori, enumerando i diversi scaffali con la stessa logica di lettere e numeri, e via dicendo.
Il futuro nella logistica è già presente. Tocca ora alle aziende voltare pagina rispetto a una logistica “vecchia” concepita su un lavoro di facchinaggio affidato a cooperative a basso costo, alla quale va preferito l’inserimento di risorse umane sempre più specializzate e in grado di interagire con ciò che la tecnologia già ci offre.