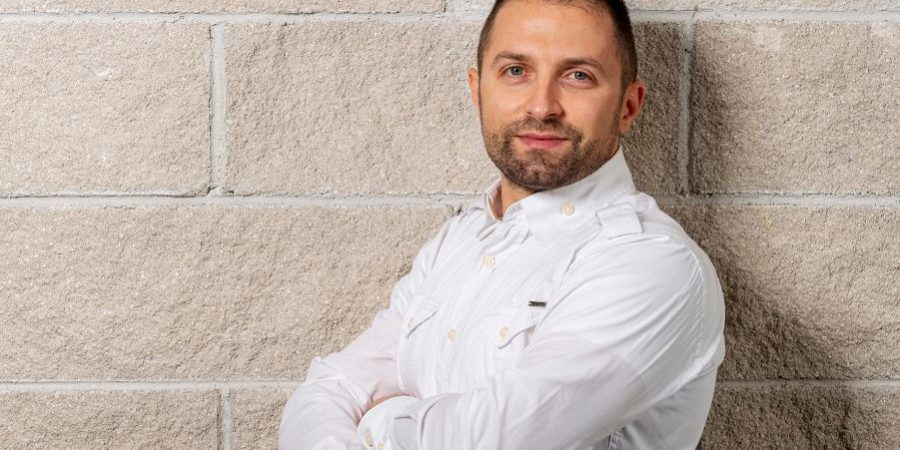
Partita negli anni ‘80 dall’idea di Sergio Paradisi, padre dei due attuali titolari, che decise di dedicarsi allo stampaggio di termoindurenti, materiali plastici al tempo poco diffusi, la traiettoria industriale di Ludabak – 6 milioni di euro di fatturato nel 2022 a fronte di 35 dipendenti – si è via via sviluppata anche su una direttrice commerciale parallela, scelta che ha portato indubbi vantaggi alla Pmi di Serra de’ Conti in provincia di Ancona. Intorno agli anni Duemila, infatti, nel periodo di crisi vissuto dall’azienda marchigiana a causa delle difficoltà che colpirono duramente aziende primarie della zona, diventò indispensabile cambiare rotta e dedicarsi anche allo stampaggio di termoplastica. “Ed è stata una decisione azzeccata considerato che ora le nostre entrate sono equamente divise tra prodotti termoindurenti e termoplastici – spiega Luca Paradisi (nella foto in alto), che assieme al fratello Daniele guida la Ludabak –. I primi sono materiali che vengono usati in situazioni specifiche, in altre parole quando è richiesta resistenza termica, isolamento elettrico e stabilità dimensionale. Hanno peculiarità per cui i progettisti, soprattutto in alcuni ambiti, li prediligono. E così per lungo tempo, orientatosi verso il mondo degli elettrodomestici, nostro padre ha fornito in particolare manopole e maniglie per forni e piani cottura ad una grande azienda del territorio”.
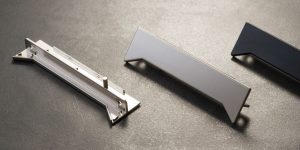
PROFILI STAMPATI IN MATERIALE TERMOINDURENTE PER SOSTITUZIONE COMPONENTE IN METALLO
Questo consentì all’impresa dell’anconetano di crescere in modo sostenibile diventando una realtà industriale strutturata con numeri di un certo livello, oltre a farsi apprezzare anche da altri clienti che operavano nello stesso settore. “Il salto di qualità venne fatto con un brevetto specifico nel campo dello stampaggio dei termoindurenti, ossia l’applicazione di una finitura galvanica da noi poi sviluppata assieme ai fornitori di materiali e che ci ha fatto conoscere ancora più a largo spettro”.
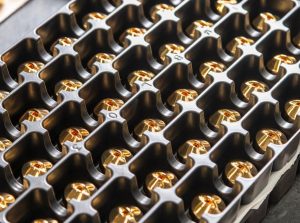
ACCESSORI CON FINITURA ORO LUCIDO DA PROCESSO GALVANICO
Dopo un periodo di grandi soddisfazioni sono però arrivati tempi sicuramente più complessi da gestire, frangente in cui sono andate in grossa difficoltà realtà consolidate del settore degli elettrodomestici e pure Ludabak ha dovuto fare i conti con la necessità di adeguare la propria offerta. “Un ulteriore problema è venuto dal cambio dell’estetica dei prodotti inseriti nei forni, che ci ha costretto a reagire molto velocemente per non restare indietro rispetto alla concorrenza – sottolinea Paradisi –. In più ci siamo mossi per trovare nuovi sbocchi commerciali per provare a diversificare rispetto al mondo dell’elettrodomestico. Per cui abbiamo inserito nuovi clienti del settore degli accessori da cucina, di quello elettrico, in cui i nostri interruttori e altri prodotti vengono usati in presenza di alta tensione, un percorso di diversificazione proseguito infine con i materiali”.
L’impegno quasi totalmente conto terzi è così continuato con l’entrata a pieno titolo anche nell’ambiente commerciale dello stampaggio del termoplastico, ma che ormai non disdegna di lanciare lo sguardo pure verso altri obiettivi. “Ci interessa molto la cosmesi, la moda legata all’impiego di accessori di alta gamma, mentre stiamo valutando l’inserimento nel nostro portafoglio di clientela proveniente dal settore dell’automotive. Vorremmo, insomma, iniziare a fornire alcune aziende della zona con prodotti stampati in termoplastica seguendo, come sempre, il disegno inviato dal committente: sia cose non in ferro e che non si vedono, come componenti per pompe o motori elettrici, ventole, raccordi presenti al di sotto del cofano della macchina, oppure materiali più ‘estetici’, vedi le verniciature o i processi galvanici ma anche pulsanti e manopoline”, chiarisce il contitolare di Ludabak.
Prodotti creati negli stabilimenti della Pmi marchigiana che vengono utilizzati in svariate zone del mondo, tra cui spicca l’Europa, con Francia, Germania e Polonia – paese dove sono andate a produrre un buon numero di aziende italiane – a tirare il gruppo, ma che sono presenti pure in Turchia e Sud America. “Adesso abbiamo deciso di ricominciare a curare anche il mercato di prossimità, cercando di guardare più vicino dopo aver lasciato per qualche tempo inesplorato il territorio intorno a noi”.
Per rendere più sostenibile il giornaliero di un’azienda molto attiva industrialmente come Ludabak, nel 2019 si è deciso di installare un impianto fotovoltaico da 250 kw in grado di garantire l’energia necessaria per coprire un terzo del fabbisogno complessivo. “Il nostro problema sta nel fatto che abbiamo turni di notte a cui il fotovoltaico non può ovviamente dare aiuto – commenta Paradisi –. Non abbiamo bisogno, insomma, di una produzione di energia di picco, ma di una costante. Nel 2024 speriamo comunque di riuscire a dotarci di un ulteriore impianto da 250 kw e nel frattempo, per essere sempre più ecosostenibili, ricicliamo il cartone degli imballi per garantirgli più cicli di vita possibili”.
Per crescere ancora, Ludabak ha ampliato la propria struttura coperta di altri 2.500 metri quadri, scelta indispensabile nell’ottica di continuare a progredire e poter così entrare nell’automotive attraverso anche l’acquisizione di presse di notevoli dimensioni.