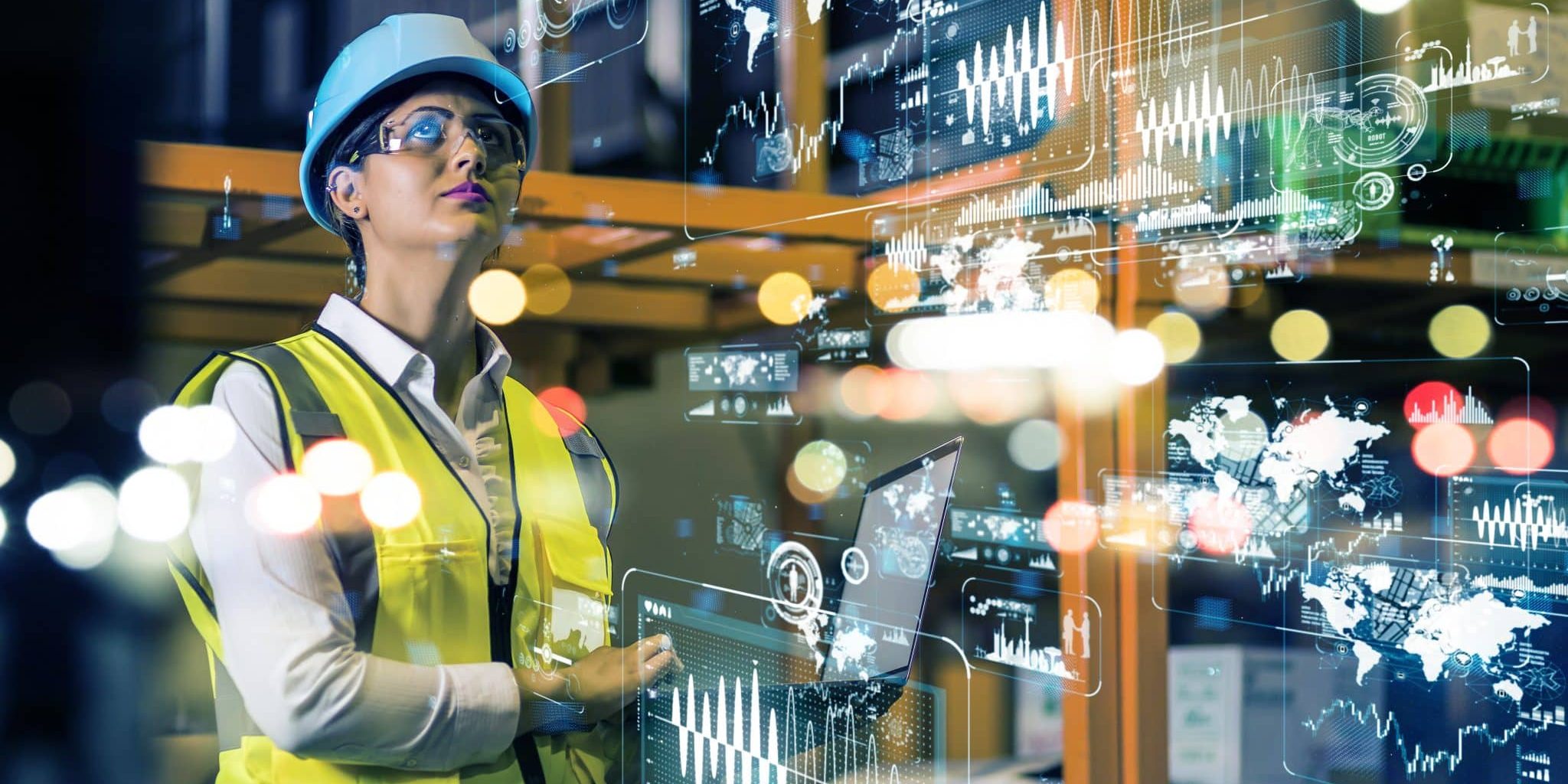
Per le imprese italiane si sta configurando un periodo difficile per via, da un lato, degli aumenti che hanno caratterizzato tassi di interesse e tariffe energetiche, con le conseguenti diminuzioni del potere di acquisto dei consumatori e della domanda, dall’altro, degli strascichi legati alla reperibilità dei materiali, che hanno portato a variazioni improvvise dei tempi e costi di approvvigionamento e delle scelte sulle scorte de detenere.
In un contesto sfavorevole sotto diversi punti di vista e in continua evoluzione, la produttività risulta cruciale per mantenere la competitività e la crescita della nostra economia. Tuttavia, secondo il rapporto Ocse (2021), la produttività del lavoro nel settore manifatturiero italiano risulta essere inferiore a quella di paesi come la Germania e gli Stati Uniti. Le imprese italiane, per la maggior parte piccole e medie imprese, si trovano in difficoltà e faticano a mettere in pratica azioni adeguate a mantenere e, se possibile, migliorare la propria competitività. Si rende sempre più necessario trattare questo tema, concentrandosi sugli strumenti che possano supportare le imprese italiane nella ricerca della produttività.
L’innovazione tecnologica è uno dei principali motori della produttività nel settore manifatturiero e le fabbriche italiane si trovano ad affrontare una crescente concorrenza da parte delle economie emergenti e dei paesi più avanzati proprio in termini di tecnologia, come la Germania e il Giappone. Se il Giappone è tra i primi paesi per uso dell’automazione, è stato anche la culla del Toyota Production System, primo esempio di applicazione della Lean Production e riconosciuto come uno degli approcci più importanti per il conseguimento della produttività delle attività industriali basato sul miglioramento continuo dei processi. Sempre nel contesto automotive, ma in Germania, si è avviata la quarta rivoluzione industriale, conosciuta anche come Industry 4.0 e basata sulla digitalizzazione di quegli stessi processi già semplificati e resi snelli dalla Lean Production.
La trasformazione digitale di Industry 4.0 comprende nove pilastri tecnologici (sistemi di produzione avanzati, manifattura additiva, industrial internet of things, cloud computing, cyber security, integrazione orizzontale e verticale, simulazione, big data e analytics e realtà aumentata/virtuale) ai quali si sono più recentemente aggiunte l’intelligenza artificiale e la blockchain.
Queste tecnologie, permettendo la connessione estesa tra macchine e oggetti intelligenti, capaci di dialogare tra loro, con l’ambiente circostante e con gli operatori, rappresentano il mezzo con cui conseguire numerosi benefici quali la riduzione di tempi e costi dei processi e aprendo a nuove possibilità in termini di operazioni finora precluse. Grazie a nuove modalità di comunicazione in tempo reale di dati raccolti dal campo, è possibile superare il limite della segregazione dei robot industriali e far lavorare i nuovi cobot (robot collaborativi) a stretto contatto con l’uomo, eliminando così l’interruzione del flusso del processo. La manifattura additiva rende economicamente conveniente la realizzazione di un pezzo unico o la realizzazione di geometrie complesse in un’unica fase. La realtà virtuale abilita l’addestramento delle persone all’uso di un nuovo macchinario prima ancora che questo sia installato nel reparto produttivo. Mostrare istruzioni e informazioni sul processo agli operatori ne semplifica il lavoro e allo stesso tempo raccogliere dati sul processo abilita il monitoraggio della fabbrica in tempo reale e la presa di decisioni sul sistema produttivo applicando tecniche di data analytics al suo gemello digitale.
I benefici non sono limitati alla riduzione dei tempi e dei costi di realizzazione, al miglioramento della qualità, del livello di servizio e della flessibilità e all’abilitare la personalizzazione, che pur basterebbero per convincersi del vantaggio portato dall’adozione delle tecnologie digitali in termini di miglioramento della produttività, ma possono estendersi fino alla realizzazione di nuove possibili modalità di creazione del valore.
Non sono rari gli esempi di costruttori di macchine italiani che hanno realizzato un nuovo modello di business trasformando la tradizionale vendita in un contratto di service, che prevede una remunerazione mensile legata al conseguimento di determinati livelli di prestazione dell’impianto (ottenuti proprio tramite le tecnologie digitali, a beneficio della produttività del cliente), modello conosciuto anche come servitisation. Altre imprese, invece, hanno conseguito la costituzione di una nuova unità di business e l’ingresso nel mercato delle tecnologie digitali a partire dall’esperienza (positiva) di adozione di queste tecnologie all’interno dei propri processi produttivi, aumentando così le occasioni di creazione del valore.
Se le opportunità sono innumerevoli, non è altrettanto vero che le implementazioni da parte delle imprese manifatturiere italiane siano oggi numerose. Anche se non sempre è utile adottare tutti i pilastri tecnologici per poter conseguire il miglioramento – specialmente nel contesto delle imprese medio-piccole l’adozione dovrebbe essere limitata a un set di tecnologie sulle quali concentrare gli investimenti e gli sforzi di implementazione –, diverse indagini, tra le quali la survey condotta dal Lean Club di LIUC Business School nel 2019 e rinnovata nell’estate del 2022, riportano come non solo le implementazioni siano ridotte in numero o portate a termine solo parzialmente, ma risultino ancora mancanti diversi prerequisiti all’adozione delle tecnologie. Tra questi vi è l’applicazione diffusa della Lean Production, senza la quale si rischierebbe di “digitalizzare gli sprechi”, che ancora fatica ad affermarsi nei sistemi produttivi italiani e, in particolare, nelle realtà più piccole.
Per superare le sfide attuali, gli imprenditori non possono perdere l’occasione di sfruttare la leva dell’innovazione tecnologica per incrementare la produttività dei sistemi produttivi, già adottata dai concorrenti stranieri. Dovrebbero valutare inoltre di implementare le tecnologie digitali perseguendo obiettivi che non si limitino alla sola riduzione di tempi e dei costi o al miglioramento della qualità, ma che si spingano fino a cogliere nuove opportunità di mercato. Il primo passo per affrontare questa trasformazione però è ricordare che, in tutto il mondo, le fabbriche “4.0” sono prima di tutto fabbriche lean.
Nota sull’autrice
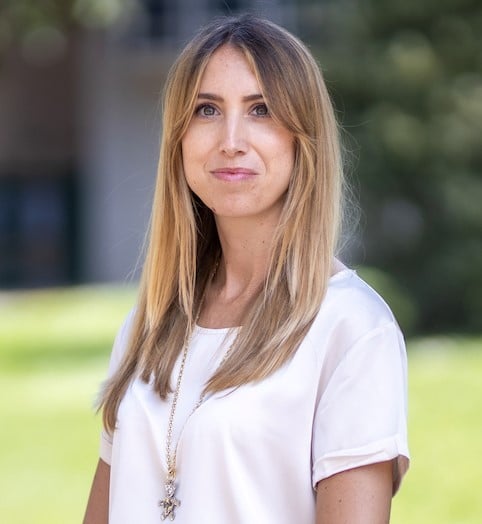
ROSSELLA POZZI
Rossella Pozzi è ricercatrice senior presso la LIUC – Università Cattaneo, Scuola di Ingegneria Industriale, dove è titolare degli insegnamenti Lean Manufacturing, Qualità: progetto e gestione e Prescriptive analytics per l’pperational excellence.
È membro della core faculty della LIUC Business School, dirige le attività del Lean Club e coordina il percorso Operational Excellence e Industry 4.0. La sua attività di ricerca si concentra sulla lean production, sulle tecnologie digitali nelle operations e i modelli matematici per la produzione industriale.