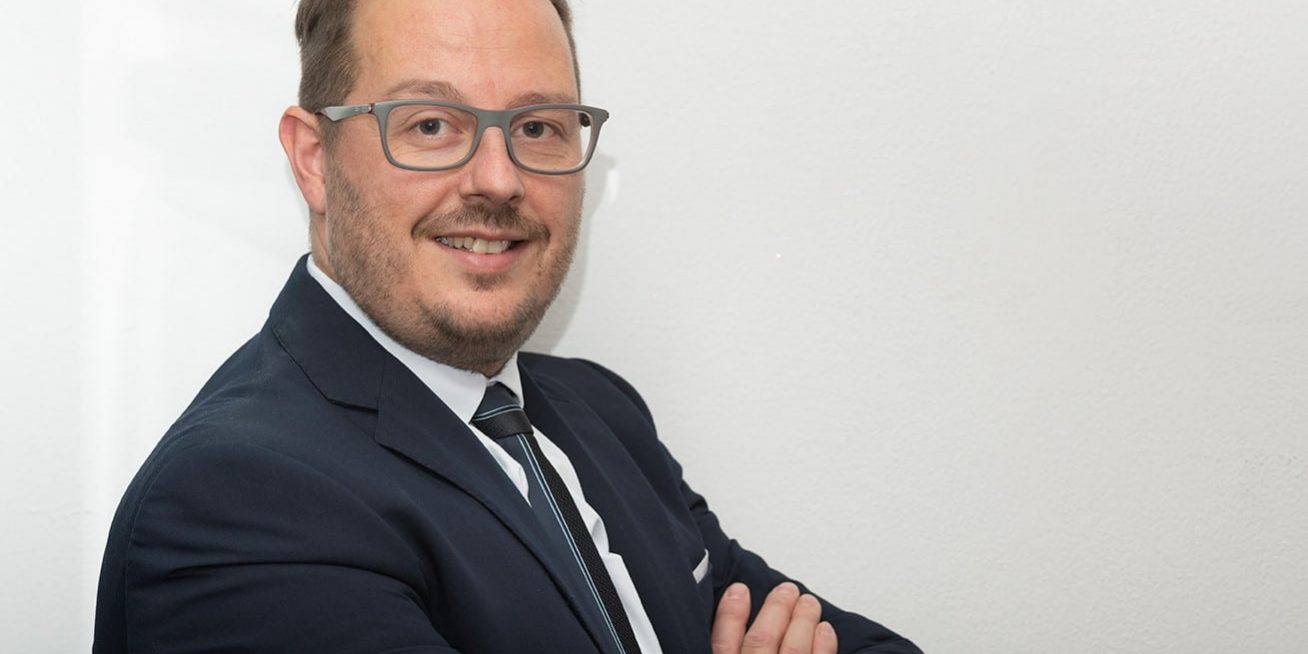

SAMUELE MAUGERI
L’ondata innovativa nascente della quarta rivoluzione industriale coinvolge anche la Mebra Plastik Italia, una realtà manifatturiera di Busto Arstizio, in provincia di Varese, specializzata nell’estrusione di tubi per oleodinamica e pneumatica.
“La nostra impresa partiva da una situazione un po’ ‘scarica’ a livello tecnologico, ma la volontà di automatizzarci per andare verso il futuro c’era e per questo, insieme con Samuele Maugeri, responsabile operations di Mebra e nipote del fondatore, circa cinque anni fa abbiamo deciso di ridisegnare in chiave 4.0 tutto il processo produttivo”. Così Nicola Marchesin, responsabile IT dell’azienda varesina che conta più di cento dipendenti.
“Oggi è tutto in un solo click ma prima, quando il cliente chiamava, si doveva andare fisicamente in magazzino per vedere se quel determinato prodotto era presente, con notevole impiego di tempo e risorse per completare una spedizione. Se poi si pensa che la struttura produttiva si estende per 33.500 metri, quasi per la metà dedicati al magazzino, si intuisce facilmente che i tempi per gestire un portafoglio prodotti, con più di 30mila articoli diversi, erano molto più lunghi”. Parole, quelle di Marchesin, che fotografano una situazione in cui si trovano oggi ancora molte imprese italiane. Non molte hanno varcato la soglia della digitalizzazione e ogni giorno sono chiamate ad essere sempre più resilienti agli effetti ciclici dell’economia.
Con l’aggravio della pandemia solo quelle che saranno in grado di seguire e adeguarsi alla digital disruption, immettendosi in un sentiero di crescita di lungo termine, potranno ritagliarsi un ruolo da protagoniste nel mercato globale che verrà. Una posizione condivisa anche dal management di Mebra Plastik che, al fine di ottimizzare i diversi processi, ha ritenuto opportuno informatizzare tutti i comparti, dal magazzino alla produzione, fino al controllo di gestione.
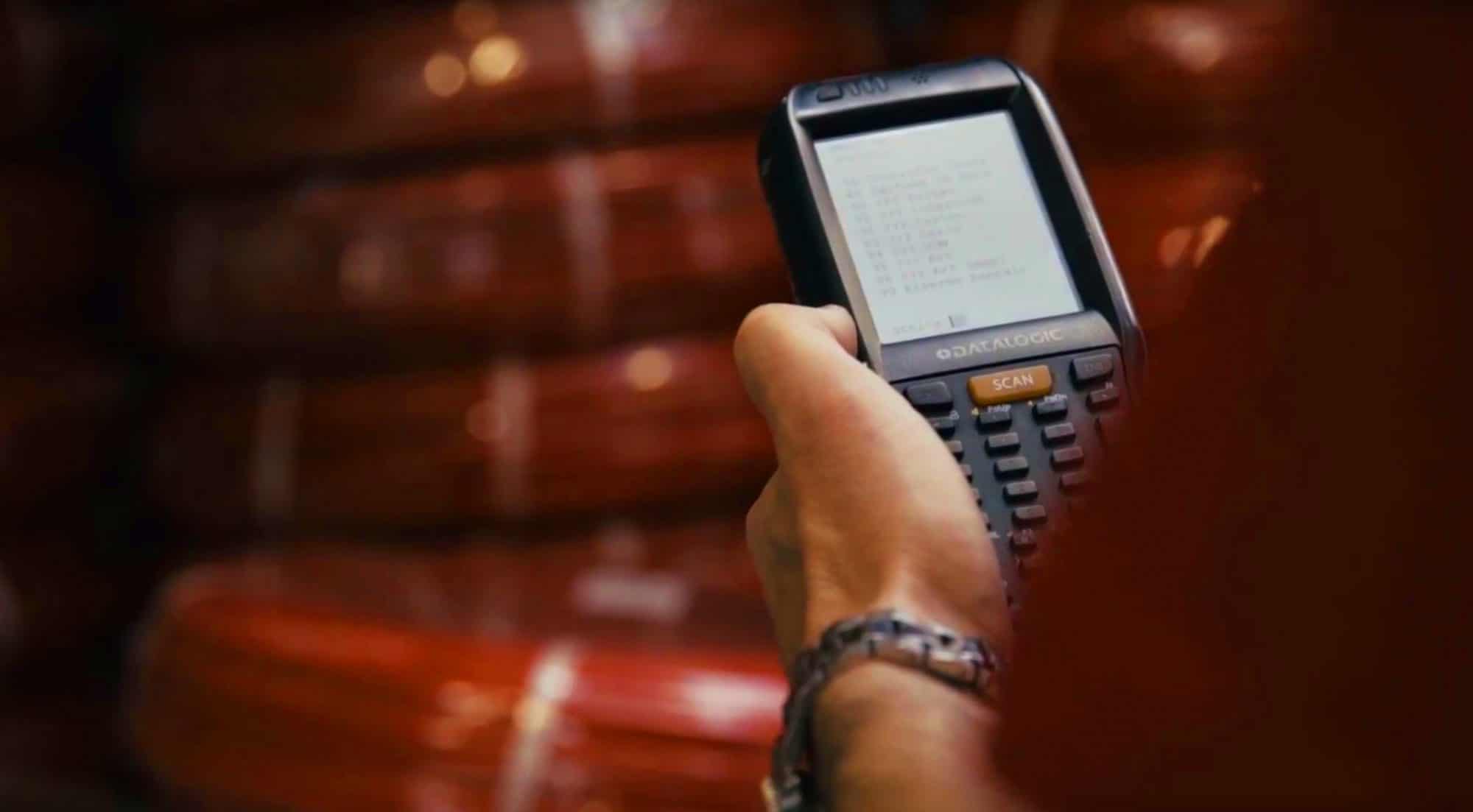
GESTIONE LOGISTICA DA PALMARE
“Il primo passo verso questo sistema all’avanguardia – racconta Marchesin – è stato l’acquisizione di un software di logistica (WMS) che ci ha permesso di utilizzare dei palmari per gli operatori coinvolti, guidandoli nella preparazione delle spedizioni nell’ottica del percorso più breve”. “Un’impalcatura informatica – spiega – che oltre ad accorciare notevolmente i tempi per la finalizzazione di un ordine, ha consentito di ridurre anche quelli per l’inserimento della nuova forza lavoro, portando la formazione, ad esempio di un magazziniere, dai 3-6 mesi di prima a un massimo di 24 ore. Un operatore inserito la mattina, con l’ausilio di questo palmare, il pomeriggio è già in grado di muoversi nel magazzino, portando anche il margine di errore nella procedura a rasentare lo zero. Il passaggio successivo nel percorso di trasformazione è stato l’acquisizione di un altro software per l’avanzamento della produzione. Una doppia piattaforma MES e APS che consente di indirizzare l’operatore nella lavorazione che sta effettuando. Quindi schedulazione, pianificazione e manifacturing execution”.
E aggiunge Marchesin “La forte interconnessione tra tutti i reparti supportata da questa impalcatura informatica fornisce numeri reali sull’andamento della produzione e su come si muove il mercato, rendendo possibili un’analisi approfondita delle performance e una pianificazione avanzata ben più precisa e proficua di quella che dovrà essere la lavorazione. Inoltre, la potenzialità dello smart working, data dall’infrastruttura, ci ha permesso di fornire una pronta risposta alla nostra clientela anche durante la fase di pandemia, quando era presente fisicamente solo il 30% del personale ed erano attive solo determinate linee di produzione”.
Innovazioni costate complessivamente circa un milione di euro e rese possibili anche grazie all’utilizzo dell’iperammortamento, ma, precisa Marchesin, “senza questa agevolazione saremmo andati comunque nella direzione di Industria 4.0, magari in misura inferiore. Certo è che strumenti di questo tipo contribuiscono a supportare le imprese, consentendo maggiori investimenti in beni ad alto valore tecnologico”.
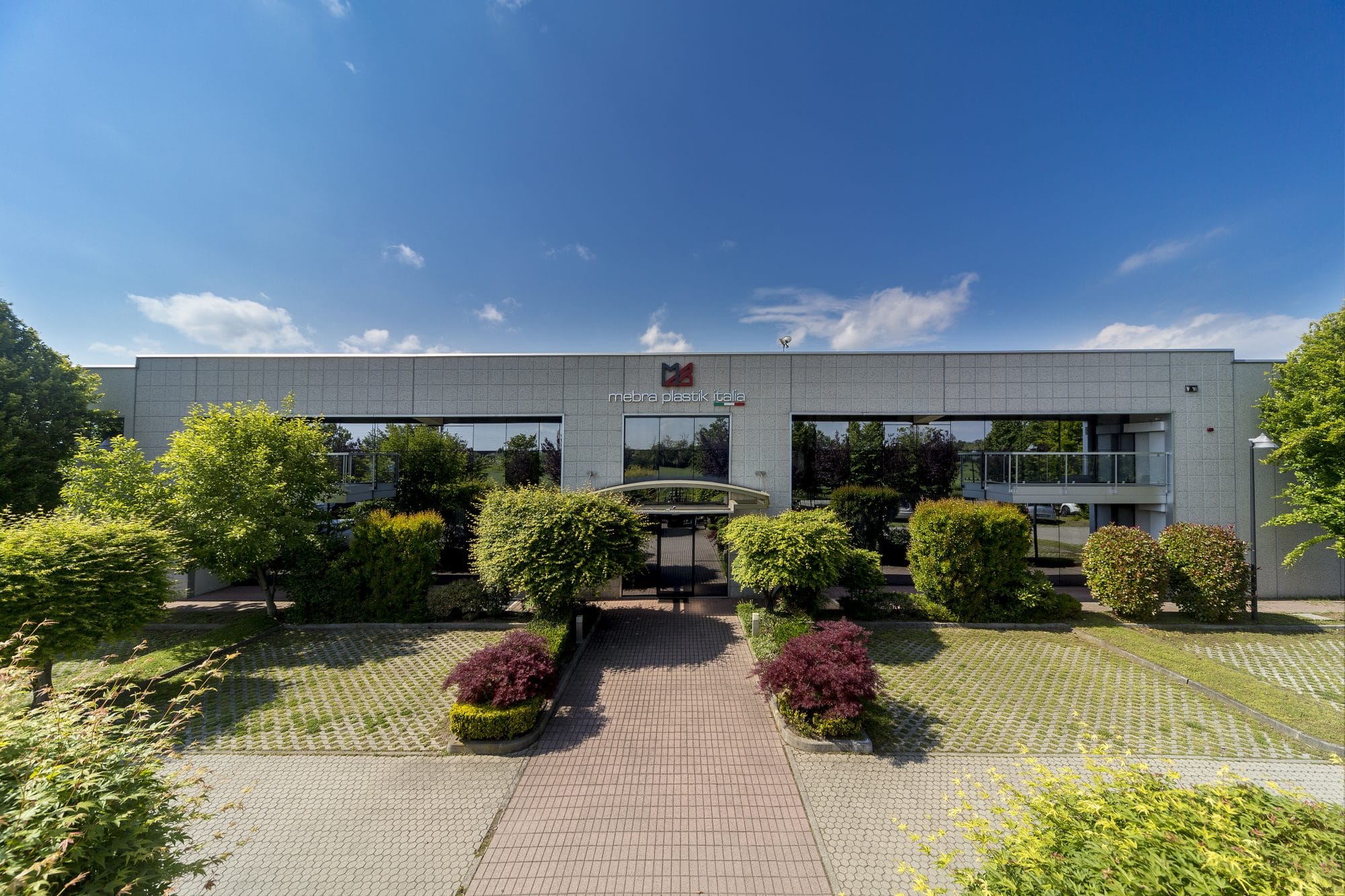
LA SEDE COMMERCIALE
Un’azienda virtuosa, la Mebra Plastik Italia, che sposa bene il binomio innovazione e sostenibilità: “Se da un lato si potrebbe pensare che abbiamo realizzato tutte le ottimizzazioni possibili, includendo anche la sensoristica e il controllo qualità – afferma Marchesin – in realtà c’è sempre spazio per migliorare e utilizzare nuove tecnologie, con tanti progetti che vanno dall’e-commerce a quelli con una particolare attenzione all’ambiente”. Ad esempio, illustra il manager, “tra le diverse azioni di rinnovamento messe in campo, abbiamo effettuato il totale relamping della nostra struttura, sostituendo le lampadine di vecchia generazione con quelle a led e generando un risparmio energetico intorno al 70%. Senza contare poi che nei nostri stabilimenti non si produce un grammo di scarti e viene utilizzata solo energia green proveniente al 100% da fonti rinnovabili”.