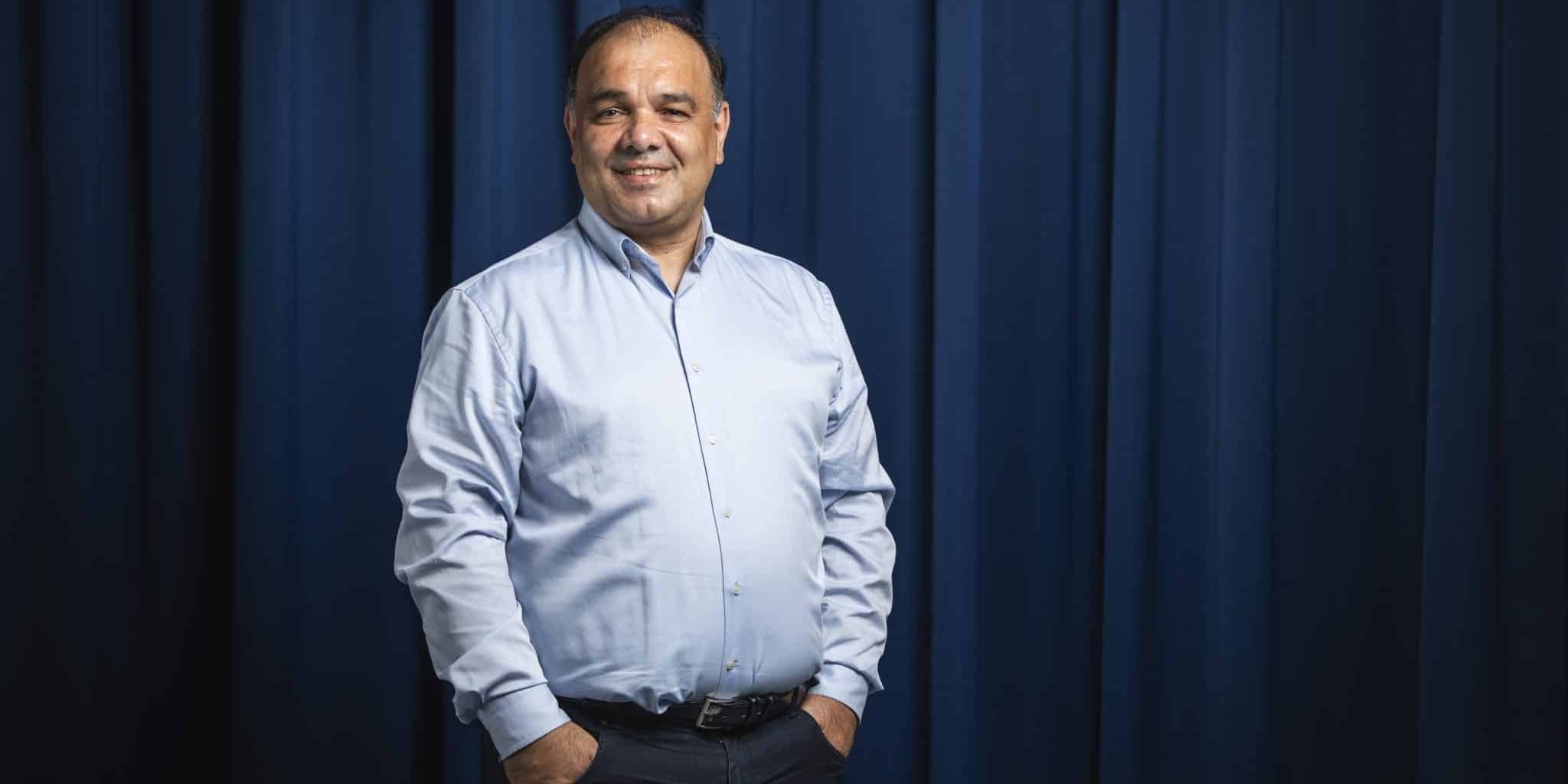
C’è l’innovazione dei webinar, fatta con le slide e qualche domanda dal pubblico, e poi c’è l’innovazione vera, fatta di incontri, sviluppo prototipi, esperimenti, prove tecniche e tanto, tanto ascolto. Su questo secondo modello ha scommesso il Competence Industry Manufacturing 4.0 (CIM4.0), uno degli otto centri di competenza nazionali voluti dal ministero dello Sviluppo economico per favorire il trasferimento tecnologico alle imprese. A Torino, dove ha sede, le due linee pilota – Digital Factory e Additive Manufacturing Metallo e Polimerico – lavorano su prodotti e processi per i settori automotive e aerospazio in primis. Ad incontrare le imprese c’è Enrico Pisino, ingegnere con una lunga carriera in Fiat e poi Chrysler e FCA, dove è stato responsabile della Ricerca & Innovazione sia negli Stati Uniti (2011-2016) che in Europa (2015-2019) ai tempi di Sergio Marchionne. Da circa tre anni è Ceo del CIM4.0 e parla la stessa “lingua” degli imprenditori.
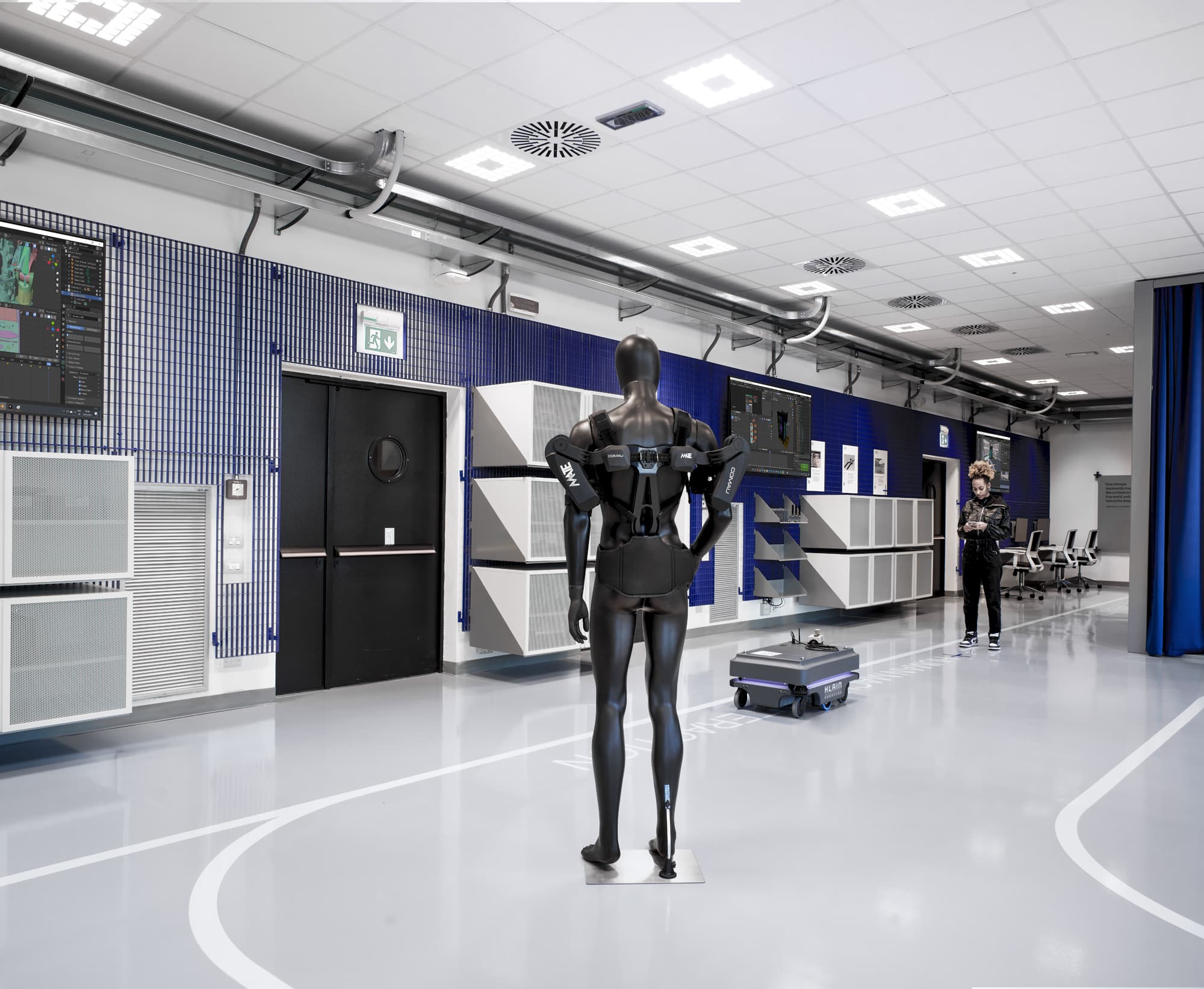
UNA VISTA DELLA DIGITAL PILOT LINE
Che imprese sono quelle che si rivolgono al CIM4.0?
Sono soprattutto aziende dei settori automotive e aerospace, in prevalenza del Nord e Centro Italia. La gran parte è di medie dimensioni, alcune sono piccole, ancora pochissime le micro e le startup. Vengono da noi perché vogliono migliorare l’efficienza dei processi produttivi e la qualità dei prodotti attraverso le tecnologie digitali oppure – nel caso della manifattura additiva – perché vogliono ridurre i costi di investimento o migliorare le performance di prodotti, attrezzature per la produzione o per stampi oppure realizzare riparazioni.
Alcune ci chiedono anche piccoli lotti di prodotti ottimizzati grazie alla stampa 3D, sia metallica che polimerica, perché magari lavorano in filiera con grandi player che hanno già adottato le tecnologie dell’Industry 4.0.
Che idea si è fatto dello stato di salute delle Pmi in fatto di innovazione tecnologica?
Il 100% di quelle che arrivano da noi è consapevole che deve darsi da fare sul fronte della transizione digitale ed ecologica ed è disposto a fare investimenti. Ho trovato tanta competenza e voglia di innovare, ma occorre instaurare un rapporto molto chiaro, che significa trovare il tempo per ascoltare e per raccontare. Tipicamente ospitiamo le aziende presso di noi e spieghiamo il potenziale delle tecnologie attraverso dei casi di uso, poi andiamo a trovarle per comprendere il loro stato dell’arte, definire le aree di debolezza e miglioramento e avviare le attività necessarie a sviluppare le soluzioni. Non esistono dunque servizi generalisti, ma customizzati sui fabbisogni specifici delle imprese.
Oggi che cosa rallenta la maturazione tecnologica di un’impresa?
Dal mio punto di vista, il primo ostacolo è la mancanza di un’offerta, ovvero di servizi dimensionati, per le Pmi. Faccio un esempio: permettere a una Pmi di vedere, toccare con mano cosa oggi è possibile fare con l’intelligenza artificiale o la manifattura additiva è una novità. Consentiamo di fare esperimenti e sviluppare applicazioni per i loro contesti. Oggi questa offerta esiste e, benché non sia ancora dimensionata per rispondere a tutte le esigenze del tessuto nazionale, rappresenta un primo passo avanti.
C’è poi un secondo ostacolo, sempre per le Pmi, legato alla disponibilità economica e di risorse da dedicare al tema dell’innovazione. Negli ultimi anni queste aziende hanno vissuto una forte razionalizzazione delle risorse, sia umane che finanziarie. Spesso non hanno la possibilità di distaccare dei collaboratori per un periodo di formazione perché il personale è saturo sulle attività correnti. Noi le aiutiamo creando quella discontinuità che consenta di formare le risorse interne, anche tramite la nostra Academy, garantendo per esempio l’innesto di nuovi tecnici o ingegneri, e di essere supportate anche economicamente nelle attività di trasferimento tecnologico.
Ci fa qualche esempio pratico di come sono state applicate le vostre tecnologie?
Certamente. Abbiamo applicato la stampa 3D metallica per sviluppare stampi per componenti in plastica destinati all’automotive. Il tradizionale stampaggio a iniezione è condizionato dal tempo totale di ciclo, che include il tempo di raffreddamento dello stampo per poi effettuare l’estrazione del pezzo. Ebbene, con la stampa 3D abbiamo realizzato dei canali di raffreddamento per nuovi stampi ad alta efficienza riducendo il tempo di estrazione del 30%. Abbiamo quindi aiutato l’impresa – la Tecno Bajardi di Torino, nel caso specifico – a trasferire questa soluzione sul mercato. Una cosa che non ha concorrenti in Cina perché, al momento, non sono in grado di replicarla.
Da questo esempio sono scaturite altre richieste e adesso siamo già alla terza applicazione della manifattura additiva con lo scopo di rendere le attrezzature più efficienti. Questo ci ha incoraggiato: raccontare casi di successo accelera la sensibilizzazione delle imprese.
Sui giornali si è parlato anche di Axel…
Sì, è il rover pensato per le attività di esplorazione sotterranea nelle gallerie senza la presenza delle persone. I test si sono conclusi con successo e grazie anche all’eco mediatica che ha avuto a livello europeo siamo stati contattati da un’importante azienda per realizzare una ispezione ancora più complessa e affascinante all’estero. Essere chiamati senza alcuna azione commerciale è una bella soddisfazione.
Il CIM4.0 è uno dei promotori del Polo nazionale della mobilità sostenibile e della manifattura, che punta a fare di Torino la capitale di un settore rinnovato. A che punto siamo?
Il Politecnico di Torino, che coordina il progetto, ha acquistato una porzione industriale di Mirafiori e la sta ristrutturando. Dentro sorgeranno centri di formazione, impianti e laboratori per lo sviluppo delle nuove tecnologie per la mobilità sostenibile destinati a supportare le imprese. Noi siamo partner dell’iniziativa e svilupperemo le linee pilota dedicate allo sviluppo dei nuovi prodotti e dei nuovi processi produttivi.
A proposito di automotive, con il rincaro delle materie prime e la corsa alle terre rare necessarie per l’elettrificazione, secondo lei il piano europeo “Fit for 55” verrà rivisto?
Potrebbe cambiare la roadmap ma non gli obiettivi e io penso che bisogna essere ambiziosi e provare a rispettare quella scadenza. Stellantis, nostro socio fondatore, creerà l’hub sulla circular economy proprio dove siamo noi come CIM4.0. Ciò vuol dire che si svilupperanno tecniche e nuovi impianti per recuperare i materiali critici e di valore con i quali oggi si producono le batterie.
In Italia a che punto siamo?
Diciamo che si sta sviluppando la filiera per l’assemblaggio delle batterie, ad esempio le gigafactory a Termoli, mentre procede meglio quella per il cosiddetto veicolo elettrificato: il più venduto in Europa è prodotto proprio qui a Torino. Quella che inizierà a svilupparsi adesso è la filiera per il recupero e il ricondizionamento di prodotti realizzati sia in Italia che in Europa. Non saremo gli unici perché la Germania si è già mossa, ma possiamo diventare uno dei player più importanti. Siamo favoriti come forma mentis e cultura: siamo fra i migliori a recuperare metalli ed elastomeri, dobbiamo diventare bravi anche con i nuovi materiali critici.
Nessun futuro, invece, per il motore endotermico, sul quale l’Italia dispone di imprese e know how di grande valore?
Non scomparirà assolutamente seppure destinato ad applicazioni limitate e differenti, magari con l’impiego di biocarburanti ottenuti in maniera sintetica oppure dell’idrogeno. Ci saranno poi paesi in cui il motore a combustione interna avrà una vita più lunga di alcuni decenni rispetto all’Europa e su quei mercati l’Italia può giocare un ruolo importante, esportando tecnologie e componenti sempre più rispettose dell’ambiente.
(Intervista pubblicata sul numero di ottobre dell’Imprenditore)
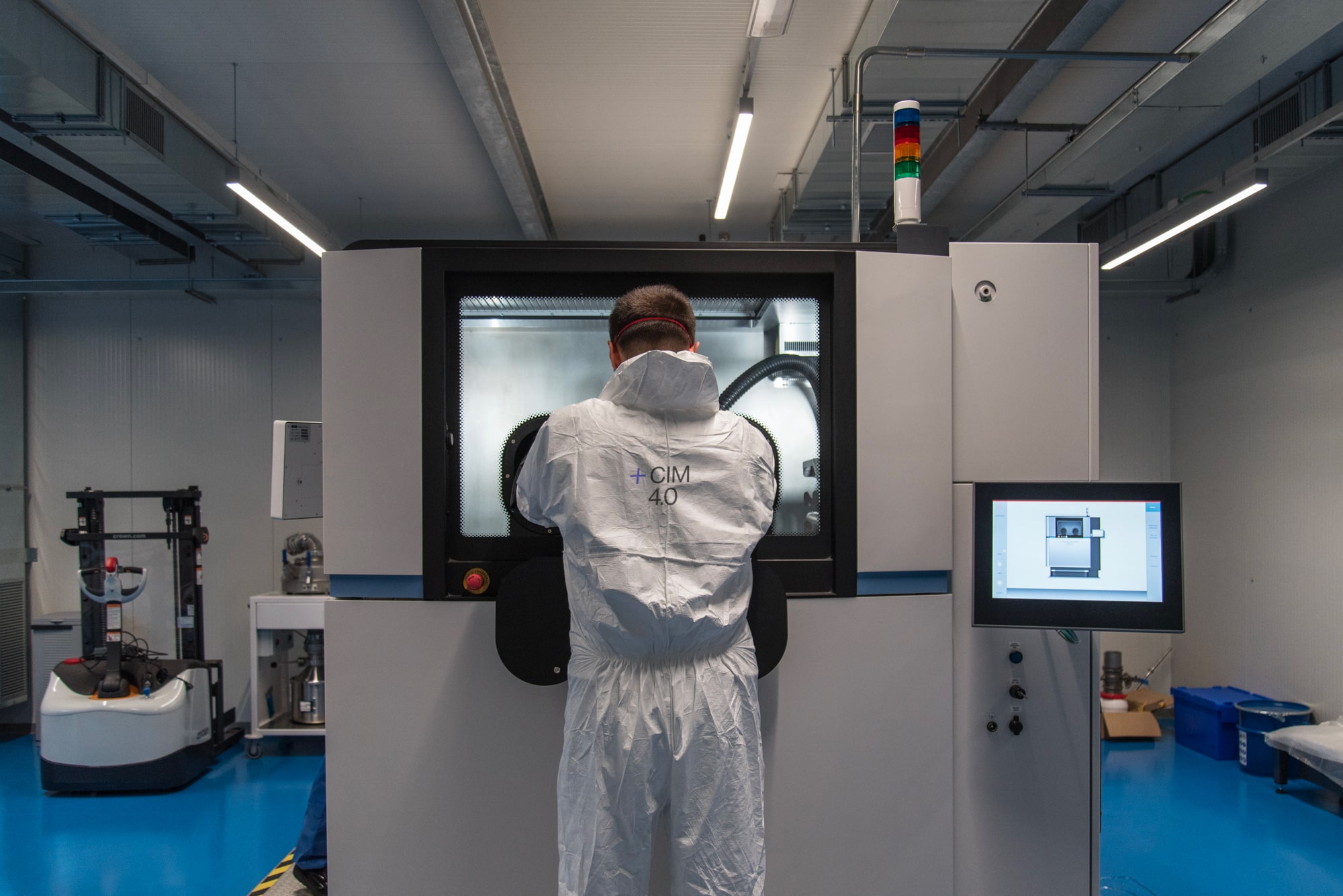
GLI SPAZI DELLA ADDITIVE MANUFACTURING PILOT LINE