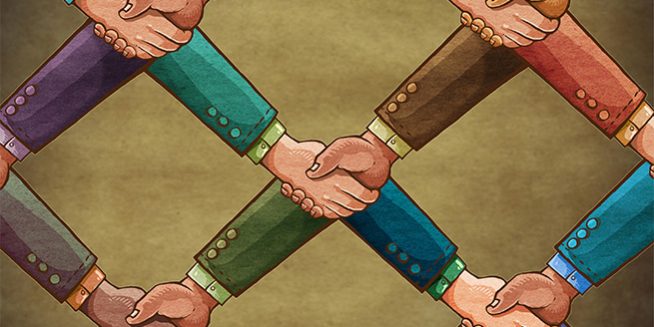
Il 20 luglio si è svolta la cerimonia conclusiva del Premio “Imprese per la sicurezza” 2015, organizzato da Confindustria e Inail con la collaborazione tecnica di Apqi (Associazione Premio Qualità Italia) e Accredia (Ente italiano di accreditamento), e rivolto alle imprese che si distinguono per l’impegno in tema di gestione della salute e sicurezza. Quest’anno, tra le vincitrici del premio anche la Diversey Italy Production, di Bagnolo Cremasco, in provincia di Cremona, azienda chimica del gruppo americano Sealed Air Corporation.
Qual è per voi il valore della sicurezza?
Belpinati: La sicurezza è un aspetto molto sentito a livello di Gruppo, infatti è uno degli elementi chiave degli obiettivi e dei valori dell’azienda; per questo motivo negli anni sono stati fatti molti investimenti supportati da differenti programmi tesi al continuo miglioramento delle attività legate alla sicurezza.
In ambito europeo, il principale indicatore che viene utilizzato per misurare la sicurezza è il Trir (Total Recordable Incident Rate), dal 2002 siamo passati da un punteggio di 4,3 all’attuale 0,47 ovvero al di sotto dello 0,5 che è il target previsto a livello europeo per l’anno corrente. Inoltre per una azienda chimica come la nostra il legame con le questioni ambientali e di salute è molto forte e questo rientra anche nella nostra visione e missione di stabilimento.
Quale percorso avete intrapreso per raggiungere standard così elevati?
Belpinati: Già prima dell’acquisizione di Diversey nel 2011 c’erano programmi e linee guida per gli stabilimenti, sia in merito all’applicazione delle norme di legge, sia riguardo agli strumenti per fare prevenzione all’interno dell’azienda. Lo stabilimento di Bagnolo Cremasco è certificato dal 1993 Iso 9001: 2008 per la qualità, dal 1998 Iso 14001 per gli aspetti ambientali e dal 2005 Ohsas 18001 per la sicurezza.
Con l’ingresso nel Gruppo Sealed Air, le iniziative legate alla sicurezza sono state accorpate ai programmi corporate. Il Safety Management System del Gruppo ha integrato i diversi programmi, per molti aspetti complementari, in un nuovo modello unificato.
La vocazione di Sealed Air e dello stabilimento di Bagnolo Cremasco è quella di applicare metodologie di continuo miglioramento che vanno comunemente sotto il nome di “lean manufacturing”, che mettono al centro il coinvolgimento dei dipendenti. Quindi anche tutti i sistemi di gestione degli aspetti legati alla sicurezza vengono gestiti con questa attenzione alle persone.
Cosa significa in concreto?
Baglivo: Uno degli strumenti che utilizziamo all’interno del nostro sistema di gestione di fabbrica è quello della registrazione delle segnalazioni di situazioni che possono essere pericolose tramite la compilazione di check list settimanali per le quali abbiamo un target di compilazione che prevede il coinvolgimento del 100% del personale. Sono delle verifiche della sicurezza dell’area di lavoro che ci permettono di andare a vedere se ci sono delle situazioni di pericolo, segnalate direttamente dalle persone che operano negli ambienti di lavoro e, conseguentemente, di attuare le opportune azioni correttive.
Come sono state recepite dai dipendenti queste attenzioni alla sicurezza? Avete incontrato ostacoli?
Belpinati: Ostacoli e difficoltà sono inversamente proporzionali al livello di coinvolgimento. Più il personale si sente parte della catena decisionale o partecipe nell’influenzare le decisioni e le attività di fabbrica, migliore è la percezione di quelle che possono essere restrizioni comportamentali o indicazioni da parte dell’azienda rendendo più facile farle rispettare ed eseguirle. Nel nostro stabilimento organizziamo ogni anno la “Safety Week”, una settimana votata alla sicurezza, il cui slogan è “La sicurezza comincia da te”.
A differenza della restante parte dell’anno, in questa settimana si definisce un filo conduttore per le esercitazioni, i training, i sopralluoghi degli ambienti di lavoro, per rinnovare l’importanza del coinvolgimento di tutto il personale aziendale.
Oltre al Prize avete ricevuto una menzione speciale per il “Fork lift blue light”. In cosa consiste?
Baglivo: È un progetto che riguarda l’interazione tra pedoni e carrelli elevatori, che è uno dei punti chiave di tutti gli ambienti operativi, dai reparti produttivi ai magazzini.
Siamo stati capofila di un’idea che poi è stata diffusa anche agli altri stabilimenti della Corporate. L’idea è quella di installare su tutti i carrelli elevatori di fabbrica una luce blu sia sul davanti che sul retro che avvisa dell’arrivo del carrello a circa quattro metri e mezzo prima e dopo il passaggio. Si tratta di un equipment aggiuntivo agli adempimenti normativi finalizzata ad aumentare la visibilità dei carrelli, soprattutto nelle zone in cui c’è più passaggio e quindi più interazione tra pedoni e carrelli elevatori.
Il progetto è stato realizzato in collaborazione con gli operatori: a fianco all’idea di installare la “blue light” abbiamo ridisegnato i percorsi pedonali all’interno di uno specifico reparto e lo abbiamo fatto coinvolgendo gli operatori stessi. È un esempio di quelle attività di coinvolgimento del personale di cui parlavamo prima: abbiamo trovato delle soluzioni coinvolgendo il personale e sviluppando le loro idee.